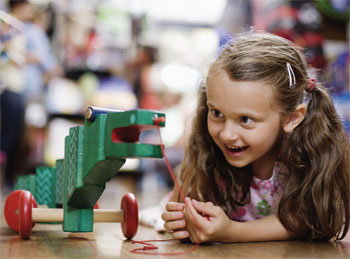
3D 프린터는 시장 진입 장벽이 높은 품목으로 아직 국내 기술력과 산업 기반은 취약한 편이다. 이미 소수의 국내 업체가 관련 시장을 두드리고 있지만, 현실은 녹록치 않은 상황이다. 본고에서는 금형 중심으로 본 3D 프린터의 제조기술 동향을 알아보고자 한다.
최근 산업통상자원부는 3D 프린터를 어떤 방식으로 적용하고 실제 산업에 어떻게 연결할지에 대해 고민하고 있다. 그만큼 3D 프린터의 파급력은 클 것으로 예상하고 있으며, 앞으로 산업 전반에 지대한 영향을 미칠 것으로 보인다. 현재 중국과 일본 등 주요 선진국은 3D 프린터에 막대한 투자를 진행 중이다. 반면 국내는 장비 기술 확보는 물론, 산업 기반도 미비한 편이다.
메탈 적층 기술 개요
메탈 적층 제조기술은 크게 3가지로 분류된다. 먼저 일반적으로 가공해 생산설비에서 절삭/연삭 공정 등을 진행하는 제거 제조(Subtractive Manufacturing)와 금형이나 사출을 찍어내는 성형 제조(Near Net Shape Manufacturing)가 있다. 마지막으로 3D 프린팅 기술 등에 이용되는 적층 제조(Additive Manufacturing)가 있다. 메탈 적층 기술은 입자 상태의 메탈파우더를 완전히(Full Melting) 녹이거나 결합제를 녹여(Partial Melting) 결합하는 방식으로 3차원 형상의 메탈 소재 제품을 제조하는 기술이다. 특히 자유롭게 형상을 제작할 수 있다는 장점을 가진다.
일반적으로 금형제조 프로세스는 아이디어와 디자인, 금형 제작 및 성형 그리고 측정 및 후가공으로 구성된다. 이때 3D 프린터 기술은 아이디어 및 디자인 단계에서 RP(쾌속조형 Rapid Prototyping, RP) 및 시제작(Mockup) 단계에 오래전부터 적용됐다. 이 방법은 제품 디자인에서 시제품 제작과 완제품의 대량 생산까지 도달하는 시행착오를 컴퓨터 기반으로 통합해 제품 생산시간을 단축할 수 있다. 한국생산기술연구원 이석우 충청권 지역 본부장은 “3D 프린터는 산업의 패러다임 변화와 3D 프린터 자체의 응용성 성숙으로 과도기에 접어든 전략 분야”라며 “제품 설계의 자유도 확대와 사용자 중심의 제품 제조, 제품화 시간을 단축할 수 있어 금형 산업에서 가장 효율적으로 사용할 수 있다”고 말했다.
장비 특성 및 소재가 관건
1990년대 말부터 RP는 이미 기술적으로 성숙했다. 산업적으로 적용이 안 된 이유는 당시 RP 기술로 제조사가 고품질의 원하는 제품을 생산할 수 있을 것으로 판단했다. 하지만 실제 RP는 장비의 특성과 소재에 따라 서로 다른 결과를 나타냈다. 따라서 서로의 요구에 맞는 장비 특성과 적합한 소재를 선택해야만 원하는 품질과 평가를 얻을 수 있다는 게 이석우 충청권 지역 본부장의 설명이다.
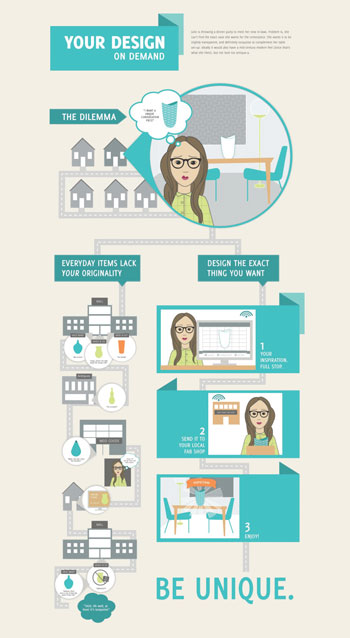
적층 방식이 가장 중요
메탈 적층 기술은 적층 방식에 따른 장비 분류와 적층 소재에 따른 분류, 접합 메커니즘에 따른 분류로 나눌 수 있다. 먼저 적층 방식에 따른 장비 분류로는 적층 소재를 노즐을 통해 선택적으로 공급하면서 3차원 형상을 제조하는 기술인 메트리얼 익스트루전(Material extrusion)과 액상의 적층 소재를 선택적으로 쌓아 올리면서 3차원 형상을 제조하는 메트리얼 제팅(Material jetting) 등이 있다. 또한 적층 소재로 분류하면 분말기반(Powder based)과 고체상태기반(Solid based), 액체상태기반(Liquid based)으로 나눌 수 있다. 분말기반에는 세미-크리스탈린 플라스틱(Semi-crystalline Plastic)과 메탈(Metal), 세라믹(Ceramic)이 있으며, 고체상태기반은 메탈 시트, 플라스틱 시트, 종이(Paper), 무정형 플라스틱 와이어(Amorphous Plastic wire)가 있다. 액체상태기반의 기술은 광경화수지(Photo-curable resins)와 몰텐 왁스(Molten wax), 필드 잉크(Filled inks) 등이 있다. 이밖에도 접합 메커니즘에 따른 분류로는 고체상태소결(Solid State Sintering), 액체상태소결 및 부분적 용해(Liquid Phase Sintering & Partial Melting), 완전 용해, 화학적 접합(Chemically Induced Binding)이 있다. 이석우 충청권 지역 본부장은 “사용자는 적층 방식을 중요하게 고려해야 하는 이유는 적층 방식의 선택에 따라 소재나 형상이 달라지기 때문”이라며 “소재의 특징은 곧 제품의 특징과 연결돼 사용자가 가장 먼저 고려해야 할 부분”이라고 언급했다.
영역 넓혀가는 3D 프린터
전 세계적으로 3D 프린터는 전략 산업으로 평가받고 있다. 수지 소재에 대해서는 기술적으로도 성숙기에 올라섰다. 하지만 아직 메탈 소재는 기술적 성장 단계로 산업에 적용하기 위해 발전할 부분이 많다. 이미 항공 분야에서는 대형 적층 공정으로 5 m 정도의 티타늄 제품과 나노급 제품을 생산하고 있다. 이밖에도 Lockheed Martin 사는 3D 프린터 기술로 항공 관련 부품을 생산해 50%의 원가 절감을 거뒀다. 국내의 경우, 카이(Korea Aerospace Industries, KAI)가 3D 프린터를 적극적으로 활용하고 있다. 이석우 충청권 지역 본부장은 “적층 제조기술은 RP 시제품을 시작으로 다양한 산업에 적용 및 제품 양산화로 전환되고 있으며, 앞으로 IT 및 우주항공산업 등의 초정밀 대형 부품으로 영역이 확대될 것”이라고 말했다. 그는 “특히 3D 프린터가 저가 보급형 제품의 상용화로 개인 3D 프린터 시장이 열릴 것으로 보인다”고 설명했다.
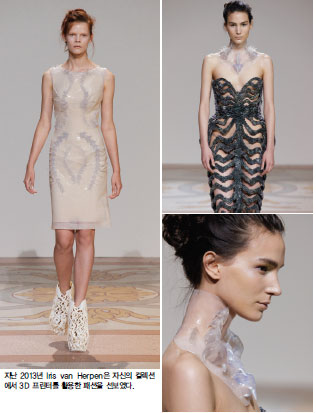
메탈 적층 기술 및 장비 현황
2012년 ASTM에서 적층 제조 기술을 7가지로 분류했으며, 그 중 메탈 적층 기술은 바인더 제팅(Binder jetting)과 시트 라미네이션(Sheet lamination), 파워 베드 퓨전(Power bed fusion),
다이렉트 에너지 디포지션(Direct energy deposition)이 있다.
Binder Jetting Process
ExOne은 바인더 제팅 프로세스(Binder Jetting Process)의 대표기업으로 스테인리스강(Stainless steel)과 청동(Bronze), 세라믹(Ceramic), 유리(Glass) 소재를 적층할 수 있다. 공정 방법은 메탈 파우더 위에 잉크젯 프린터 헤드를 통해 결합재를 분사해 적층하고, 후처리로 소결을 시행한다. 125 mm Cube 형상제작을 기준으로 10 ~ 24시간 정도 소요되며, 적층 완료 후 표면조도는 300 um(RA) 정도이다. 또한 적층할 수 있는 최대 제품 크기는 780 mm x 400 mm x 400 mm이고, 200 mm 적층 기준으로 약 ±1.5 mm의 형상 정밀도를 가지고 있다.
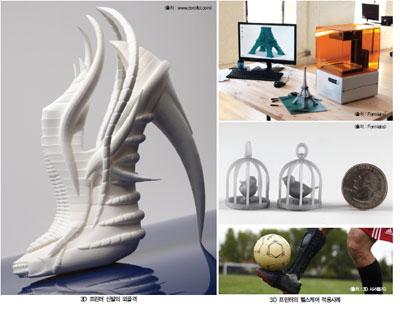
Sheet Lamination Process
Fabrisonic는 UAM(ultrasonic additive manufacturing) 방식의 대표 기업으로 알루미늄(Aluminum)과 구리(Copper), 스테인리스강(Stain
less steel) 소재의 적층이 가능하며, 두 개 이상의 이종 금속의 적층도 가능하다. 공정 방식은 25 mm x 0.1 mm 금속 테이프를 내장형 CNC로 원하는 형상으로 전달하고 초음파 용접방식으로 적층한다.
또한 125 mm Cube 형상제작을 기준으로 24시간 정도 소요되며, 적층 완료 후 표면조도는 15 um(Ra) 수준이다. 적층할 수 있는 최대 제품 크기는 1289 mm x 1829 mm x 914 mm이고, 형상에 따라 약 ±13 um의 형상 정밀도를 가진다.
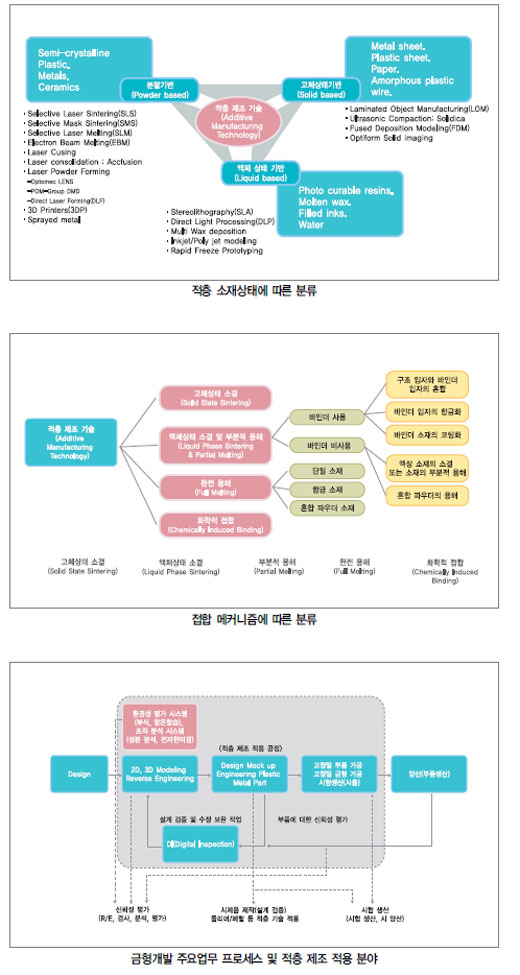
Powder Bed Fusion Process
독일의 EOS는 레이저 기반 메탈 적층 제조기업의 가장 큰 시장 점유율을 차지하며 대표적인 모델로는 EOS M 계열 모델이 있다. 400 W 급의 섬유(Fiber) 레이저를 이용하고, 최소 20 um 정도의 레이어 적층 분해능을 가진다. 또한 125 mm Cube 형상제작을 기준으로 24 ~ 48시간 정도 소요되며, 적층 완료 후 표면 조도는 9 um(Ra) 수준이다. 주요 소재는 코발트(Co) 합금과 니켈(Ni) 합금, 스테인리스(Stainless) 소재 등이 가능하며, 적층할 수 있는 최대 제품 크기는 250 mm x 250 mm x 325 mm이다.
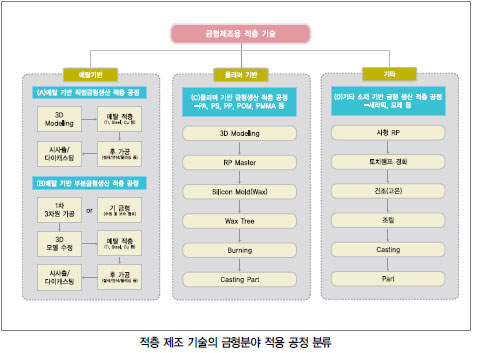
Direct energy deposition
BeAM은 레이저 클래딩 방식의 일종인 EasyCLAD 방식의 대표적인 기업으로 코발트(Co) 합금과 니켈(Ni) 합금, 스테인리스(Stainless) 등의 소재 적층이 가능하며, 두 개 이상의 이종 금속을 적층할 수 있다. 4000 W급의 레이저를 이용하며, 125 mm Cube 형상제작을 기준으로 6시간 정도 소요된다. 적층할 수 있는 최대 제품 크기는 1500 mm X 800 mm X 800 mm이고, 100 um 정도의 레이어 적층 분해능을 가지고 있다.
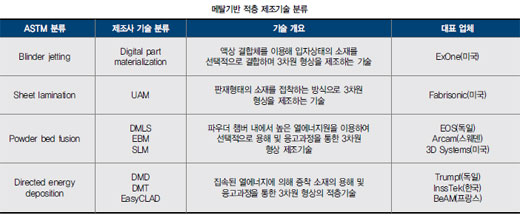
국내외 시장현황
전 세계 적층 제조 시장 규모는 약 22억 달러(2012년)이며, 이중 한국의 시장 규모는 약 0.40% 수준이다. 국가별 적층 제조 장비 활용률(장비 누적 설치 비율)은 한국이 1.9%로 중국과 일본의 6.5%, 10.2%보다 시장 기반이 미흡하다. Wohlers 보고서를 보면 2012년 산업용 장비 중 메탈 적층 시스템은 약 200대의 장비가 판매됐다. 이석우 충청권 지역 본부장은 “자동차와 항공, 금형 등의 제조산업 및 의료분야는 적층 제조방식으로 생산 기술 패러다임이 변하고 있다”며 “그중에서도 메탈 적층 제조의 중요성이 확대하고 있다”고 말했다.
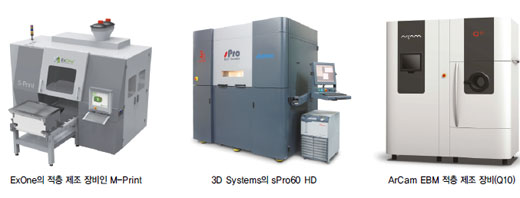
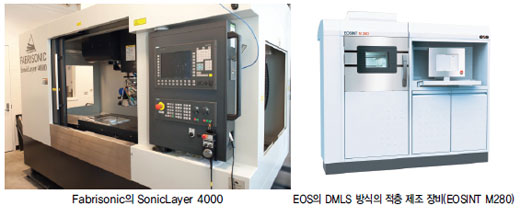
발전 전망
메탈 적층 기술 적용분야는 금형 이외의 항공과 군사부품 등 그 활용도가 확대되는 추세로, 정부 차원의 기술지원과 맞물려 발전을 거듭하는 중이다. 또한 단순한 3차원 형상의 정밀도를 다루는 수준이 아닌 슈퍼얼로이 등의 신소재 개발 및 기능성 부가 등이 가능해 기존 재료제거 공정보다 소재 낭비가 거의 없는 저가형 공정이 가능한 수준을 목표로 연구되고 있다. 이미 BBC 뉴스는 메탈 적층 제조를 통해 3,000도 이상의 초고온에서도 견딜 수 있는 복잡한 형상을 한 신소재 합금제품을 만드는 데 성공했다고 보도한 바 있다. 이렇듯 최근 메탈 기반 적층 장비 시장은 연간 15% 이상 확대되고 있다. 하지만 국내의 메탈 기반 적층 기술의 연구개발은 매우 부족한 상황이다. 따라서 앞으로 2 ~ 3년 후, 지금의 폴리머 적층 기반 장비 시장과 같이 지적 재산권 등 원천기술 확보가 어려워질 것으로 예상된다.
이석우 충청권 지역 본부장은 “메탈 적층 제조시스템은 장비와 공정 및 SW 기술 이외에 공정 노하우, 소재연구 등 상당히 많은 기술축적이 이뤄져야 한다”면서 “아직 국내는 인력과 기술력이 부족하지만, 정부와 기업에서 관련 산업에 적극적으로 투자해 광범위한 산업분야에서 사용될 것으로 보이는 3D 프린터 시장을 공략해야 한다”고 말했다. ES
<저작권자(c)스마트앤컴퍼니. 무단전재-재배포금지>